John
Welsford's website
A few of John's designs:
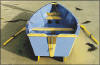
Golden Bay/Setnet
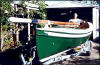
Houdini
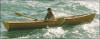
Jonsa
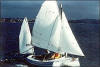
Navigator
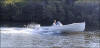
Rifleman
|
From the Drawing
Board
(occasional ramblings of a Small Craft
Designer)
by JohnWelsford
It's good stuff!
Once upon a time we could buy plywood made from perfect
veneers of durable species of wood. The best trees were selected as
suitable for plywood, and any that did not make the grade would be sent
off to be sawn up for planks. Perhaps that is a generalisation but in
reality, that would happen more often than not. I've worked in plywood
factories, not hands on down on the line but in engineering the machinery
and in working out process controls and management systems. I can tell you
that as the machineries ability to recover useable sheets of veneer the
financial side of making plywood has changed from having to use only
really top logs ( or "bolts" as some know peeler lengths) to being able to
produce a high dollar value product from a much cheaper raw material.
New types of veneer lathes can cut a thin sheet from logs
with monster knots in them and turn right down until they are into a
softwood logs juvenile core wood, new driers can dry wood of varying
densities to acceptable standards of moisture content, there are
absolutely wondrous machines that "read" faults in a sheet of wood, cut
them out and join up the pieces into continuous sheets again. Filled glues
are able to bond much larger gaps so the ragged surface finish of some
veneers is no longer an issue ( the local plywood mill here is the biggest
user of hard baking flour in the district, and they don't use it to make
cookies for lunchtime either).
The result is that plywood aint wot it used to be! It is
more than adequate for most uses, and housing, packaging and industrial
uses soak up more than 99% of the worlds plywood production. We, building
boats from the stuff are both the most demanding and the smallest user of
what is really a miraculous material for the home boatbuilder.
Where else could I find a material for my clients that
-
They can normally buy locally right off the shelf.
-
It comes in sheets that are not too hard to carry and
lift.
-
There are wide range of thicknesses and strengths.
-
Its strength is almost uniform in two out of three
planes and it is flexible enough in the other to bend around the side of
a boat.
-
That they can shape and drill with tools that they are
easily obtained and that they are usually familiar with.
-
That can be bonded by screwing, nailing, fiberglass
taping, epoxy glues, phenol formaldehyde glues, polyurethane glues,
silicones, melamines, and so on.
-
It can be painted with a paintbrush and even with
ordinary housepaint it seems to survive pretty well.
Its good stuff!
Well, in theory at least.
But the quality is an issue, like I said, apart from a very few specialist
mills the industrial and house building users drive the quality, and often
the product that suits them doesn't suit us. So what do we do? Welding our
next boat up out of aluminium or steel would be one thought, but running a
9inch angle grinder on a steel chine at 10pm while your neighbour is
trying to get the new baby to sleep is perhaps a risky option. Ferro
cement is not the material of choice for builders of sea kayaks, and a
degree in chemistry plus a 20 ft long autoclave is going to take longer to
acquire than we'd like seeing as our dreamship is to take us cruising next
summer.
So what to do?
Well, there are some good things in amongst the doom and
gloom. First though we need to have a good think about what is we actually
need.
Assuming the basic properties of plywood we need a waterproof glue bond.
The red or almost black glue line will be Phenol Formaldehyde glue, (
resorcinol) as waterproof as you will get. If in doubt buy one sheet and
take it home, write down the makers name and grade type so you can buy or
avoid that manufacturer in the future, slice a couple of bits of a corner
and boil it for a couple of hours.
If it hangs together you'll know that you can sail your
boat through boiling water with no risk of the ply delaminating. But
better still you can be pretty sure that the glue will not soften and let
go when in normally cold water.
We need one good side. It doesn't have to be perfect as
long as it has a smooth surface. This surface can be partly filler as in C
Pd grade where one side is plugged or patched. The smooth side goes
inwards, we can deal to the outside later.
Not too many internal voids. Have a look at the stack of
sheets in the rack. If some of them have a lot of gaps in the crosswise
veneers don't buy the ones that look ok, remember that only the voids near
the edge will show, and if some of sheets in a production run are ratty on
the edges, chances are that there are internal voids as well. These voids
are weak, often are a sign of poor gluebond, can reduce strength and make
a sheet bend unevenly when wrapping around a boat and the outer veneer may
collapse under impact making a hole in the surface. In some cases they are
starting places for rot. Try another grade or manufacturer.
Check for overlaps in the internal veneers, this is not
unusual in the construction or utility grades, and usually occurs where
the two half veneers that form the crossband are overlapped when being
laid up into a ply sheet. It shows in the edge as a double up at the join
about halfway along the sheet and in the surface as a change in the
appearance of the sanded surface caused by the finishing machine sanding
off the bump. This double up will appear in the finish of your boat. No
matter how much you sand it, it will eventually reappear. Wood moves ever
so slightly with time and change of moisture content, and the compressed
wood in that double up will swell slightly more than the wood around it,
it will become an unsightly straight lined bump in the finish that you
will never be able to get rid of. Ok perhaps in a bulkhead or seat top,
but Murphies law will ensure that it is the sheet that goes on about
halfway along the otherwise perfect side of your pride and joy!
Pull a sheet partway out of the rack and swing down on the
end, sight along it while holding it bent. The bend should be even, no
flat spots and sharp bends. Those indicate that some parts of the sheet
are stiffer than others, and conversely some are weaker. They should be
even!
When you are faced with a sheet of ply that reveals a gap,
or gaps in the edges, after cutting out a component use a sharp chisel to
peel some veneer off a piece of scrap, dip it in glue and drive it as far
into the void as you can. The intention being to fill the void as well as
possible preventing weakness and the accumulation of moisture.
Wood species, the old durable species are hard to come by,
so we have to make do to some extent. The fact that Gaboon, or Ocume is
widely used in boatbuilding is an indication of just how good our coating
systems are, as these two wood species can rot as quick as look at you.
Our paints, and sealants when appropriately used are very effective at
keeping water out. Rot of course needs food ( the cellulose sugars in the
wood) Oxygen and moisture, deny one of those three and rot cannot
flourish.
So we can preserve the less durable species, and while it
is nice to have a really good plywood made of a durable timber species it
is not always obtainable so we have to do our best with what is available.
I am frequently asked about treated plywood. There are
several kinds, LOSP is common, Light Oil Soluble Preservative. This stuff
is moderately effective in preservation of wood , but can be very dodgy to
glue. I myself will not use it with conventional glues and my testing has
given variable results. LOSP is normally clear, and may not be detectable
by colour or touch. It may in some cases be detectable by smell, but don't
bet on it.
Very occasionally you might come across some green LOSP
treatment. The green stain will normally be a light, bright green as
opposed to the dull, muted green of the CCA treatment chemical.
CCA ( copper, chrome, arsenic ) sounds really hazardous, but in use the
stuff bonds chemically to the wood fibre and people who have worked with
CCA treated woods for many years seem to show no signs of poisoning from
it. It is a waterborne treatment that penetrates some woods very well, and
kills anything from rot spores to teredo worm. It will not leach out, and
is very effective at preventing rot or insect damage. I suspect though
that the perceived hazard of introducing this brew of chemicals into the
environment will soon see it become unavailable.
I have built a number of boats from CCA treated
construction ply, and have found that as long as I scrub the surplus
treatment salts out of the surface of the wood with a strong solution of
bleach and hot water, I have had no problems with glueing with either
Epoxy or Resorcinol. Following my selling her the original Hobo sat quite
a few years part full of fresh water and dead leaves, and when the current
owner stripped her he found that the plywood was fine, but much of the
solid wood was history in spite of epoxy coating and lots of paint.
Pre coating is a good idea where quality is suspect. It is a good idea
anyway, but especially so when the surface finish of the ply is not good.
Rot flourishes in corners, cracks, voids and other places
where it can hide away unseen until it has a grip. This is at lease partly
because those places retain moisture, and so a rough finished surface, or
one with the checks and splits common to rotary peeled veneer. ( Peeled
from the surface of a log rotated against a lathe knife, this cylindrical
shaped sheet is then pressed flat during the drying process and will then
have a myriad of tiny lengthwise splits built into it. Some species are
affected worse than others in this process).
To reduce the chance of this happening we can use the
outstanding virtues of epoxy resin. It seals, it sticks, it fills and it
is as nearly waterproof as anything that we are likely to find. It sticks
to itself very well, so we can precoat the plywood that will be hard to
access when the boat is built. Lay the sheets out, get the number one
helper mixing resin, put the respirator and the Nitrile gloves on and
pitch into the sheets with a short nap paint roller. One coat plain resin,
and a second coat with enough microballons to make a good thick film
should do the trick. Try it at about runny porridge consistency. The
second coat should go on just as the first one has almost lost its
tackiness, and when the whole lot is well hardened the lot should be
sanded until a "Flatted" surface has been achieved.
Now I say "Flatted". That does not mean level, or in a
single plane or whatever the strict dictionary definition is. It does mean
that all of the shiny surface has been sanded to a dull, or "flat"
surface. Don't attack it too hard, or with anything much more aggressive
than about 80grit as you will make holes in the coating and have to start
again.
The objective here is to have a nice smooth surface to
which epoxy glue will adhere, and which will take paint. This is an ideal
interior surface, already sanded smooth, easy to mark with pencil or felt
pen, tends to saw without as much splintering of the cuts and is precoated
with the base of the boats preservative system. You can do both sides of
all the bulkheads, seats, bunk fronts and so on. This saves an awful lot
of time and is less wasteful of resin than you might think as you will
tend to use the ply scraps, and doing large areas in a controlled manner
is more efficient than coating a series of smaller, less accessible areas
in a partly assembled boat. ( No dribbles or puddles)
Precoating can be bought, we have a product called MDO here, sold as "Signply"
or whatever, most plywood vendors sell a grade which has one or both sides
covered with a layer of overlay. The product is intended for use as signs,
has to be durable in exterior use ( waterproof and so on ) has to be very
smooth, provide a good base for paint (where paint will stick so will
glue) and tends to be of good grades of veneer as failures are right out
there where they are easily seen.
I like MDO, short for Medium density overlay, it is
usually high grade Kraft paper impregnated with a resin such as Melamine
Urea Formaldehyde and hot pressed onto the ply surface. Its very good
stuff and in terms of saving labour and paint is often well worth the
extra price.
Even further on the precoating thing, but not so much concerned with the
finish or rotproofing, I have on occasions specified ply panels pre coated
with fibreglass, kevlar or carbon cloth or tape to improve strength. It is
easy to coat the outside of a boat during construction, but a nightmare to
do the same to the inside. I find that it is possible to better than
double the stiffness of a panel by coating both sides with "eglass" or
"unidirectional rovings" or "knitted" fibreglass fabric). To coat both
sides then try and wrap the resulting sandwich around a curve is asking
for trouble as it will be unbelievably stiff. Do the inside only as you
will find only a very slight increase in stiffness when bending toward the
coated side, and when the panel is in place and the boat at the
appropriate stage then the outside can be coated completing the sandwich .
Tough? I used 6mm ( 1/4in) Gaboon with 9oz "unis" each
side for the deck on a small ocean race that had up to three crew dancing
on the deck and although the larger unsupported panels flexed a bit that
boat did over 20,000 sea miles without so much as cracking the paint.
Just a thought, don't coat one side of a panel with Kevlar or Carbon cloth
and try to cut it with a jigsaw or sabre saw. This stuff needs special
tools to cut it and you are better cutting your panel to its finished
size, then laying up the reinforcing coating before fitting it into place.
As with most exotics it pays to read the makers instructions before using
it. Strong though!
So we can with care and work use most grades of plywood, we can improve
some that are not so good, we can make it stronger, preserve it, improve
its finish and its resistance to checking, we can indeed make a silk purse
out of a sows ear. But before you do, think about the boat, its intended
use, and its expected life. Don't over specify the product. If you are
building an ocean racer that will have an expected life of fifty years and
more in her cruising retirement, where weight and strength is an important
consideration then your choice will be quite different to the one that is
appropriate to a one sheet punt for the kids to paddle on the dam on
Granddads farm.
John Welsford.
Designer.
jwboatdesigns@xtra.co.nz |