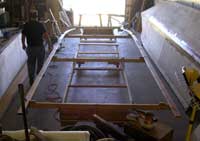 |
When we left our intrepid boat builder, Jim
had just finished the bottom sub assembly (in the picture
at left on the right) and now was ready to "go 3D".
The first chore was to set up the "shelves" on
the strongback. (click images for larger view) |
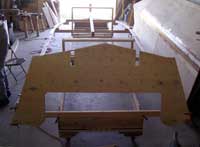 |
The transom was then set on the strongback and a couple
of temporary braces were set up to hold the stringers. |
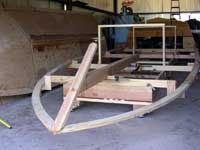 |
Here you can see the stem post with it's temporary brace
back to the strongback. Note the forward "shelf"
support allows them to dip to the proper shear shape before
meeting at the stem. |
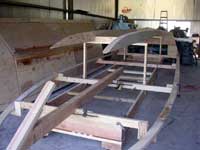 |
Here the Versa-Lam beams have been set in place on the
transom and temporary supports. These stringers have been
shaped after being ripped from a single stick. |
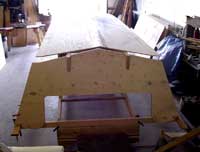 |
Now the bottom sub-assembly is set on the stringers after
they were epoxied to the transom. |
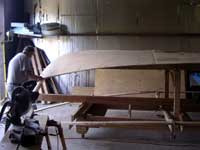 |
Here Jim fits the stem to the bottom sub-assembly. Everything
went together beautifully thanks to the clear instructions
in Renn Tolman's book. |
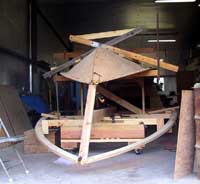 |
To make sure the bottom sub-assembly fit against the stringers,
we made a Rube Goldberg sort of clamp with 2 x 4's and pipe
clamps. It looks awful, but it did the trick. |
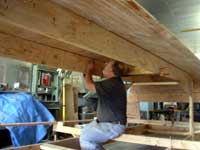 |
With the front clamped in place and the rear of the bottom
screwed to the transom, Jim spiled, or marked where the
beams met the bottom. Then the clamps were released, screw
holes were drilled, epoxy was applied, and the bottom was
glued to the stringers. |
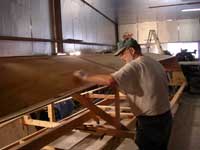 |
You may remember from our last episode that the forward
part of the bottom was 1/4" ply while the rest was
1/2". This meant that Jim had to laminate the other
1/4" onto the forward area. Here he spreads epoxy onto
the bottom with a squeege. |
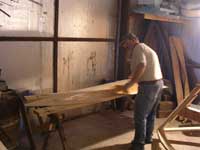 |
Here he spreads resin on the extra piece that has already
been cut to fit. The reason this is done in two pieces like
this is that a single 1/2" sheet of ply would not easily
bend into the proper shape. |
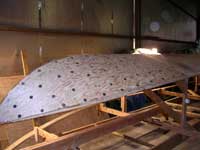 |
Here you can see the screws and fender washers that are
holding the laminated pieces in place while the epoxy cures.
Jim WD-40ed the screws beforehand so that they could be
withdrawn. Since they were to be removed, he used screws
that protruded through both layers. |
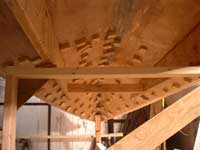 |
It's a good thing he did, too, as many of them spun out
in the 1/4" ply and had to be backed up with scraps
of 3/4" ply in order to hold. |
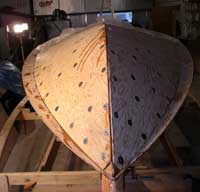 |
Here is a view from head-on. Jim is building this Jumbo
version a bit longer than the book shows which is why you
see the tiny gap where the two top pieces join the stem.
No problem, he will fix that with some thickened epoxy a
little later on. |
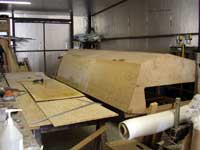 |
After that bottom, the sides are a piece of cake. The
aft sections of the sides are scarfed from two sheets each
on the table on the left of this photo. They are then glassed
on the inside (see post
1) and glued to the bottom and "shelves"
with the glass to the inside. |
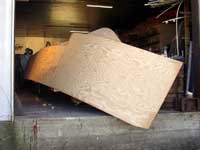 |
Next the bow side sections are presented to the boat for
spiling. Notice that he had to open the shop door to make
room. |
|
With a few screws holding this piece in place temporarily,
Jim marks where to cut this sheet of ply so it will fit. |
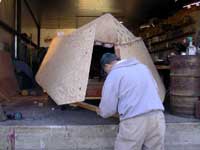 |
Just a few minor adjustments, and we close the door
on this chapter of our adventure.
Next month - glass the bottom, paint, and turnover. |