Exterior beams, rails, and moldings
have many uses on small boats.
They reinforce decks and cabintops and
still allow a smooth surface on the underside, which means a cleaner look below,
more room, and less head banging than
interior beams. Exterior beams also make
the interior much easier to finish. On
small hulls such as dinghies and dories,
girder-type exterior beams serve as bottom protection and reinforcement, tie-down and lifting handles, and safety
handholds (Fig 1).They can be installed
on wood, glass, or metal hulls.
Figure 1
There are various types of exterior reinforcements, from small toerails laid
across the deck to massive laminated
girder-type beams that can provide very
strong support, such as near a mast. Exterior reinforcements can also be in the
form of traditional grabrails that provide
support with light weight and are useful
for tying off oars, dinghy fenders, and
other gear. These deck and cabintop
beams also provide good footing and are
particularly useful at night to help in
locating yourself on deck or cabintop.
Exterior beams may be located fore
and aft, athwartships, or diagonally. Fore
and aft beams are more traditional. They
are often used for stowing oars and boathooks on deck, or routing rainwater for
catchment. They can also route sail control lines to the cockpit, and rigged with
lengths of shock cord and tie-downs, they
are very handy to hold the various odd
and assorted pieces of gear necessary on
small boats.
Athwartships beams are more out-of-the-ordinary but probably provide better
reinforcement to the deck and cabintop
since they usually extend from one sheer
clamp or carlin to the other. Though not
as aerodynamic, when properly designed
and built, they look appropriate on most
modern hulls and can be very convenient
for storage. They are also sometimes easier to build than other types.
It is often possible to design exterior
reinforcements to accomplish multiple
jobs. We once built a set of girder-type
beams laid athwartships across the cabin-top. They had holes cut for stowing two
large sculling oars and a long boathook,
and also acted as a cradle for the hard dinghy carried upside down atop the
cabin. The dinghy sheltered a ventilation
hatch in the cabintop and also protected
the varnished sculling oars from sunlight
and weather.
Girder-type beams are much stiffer and
can be less than half the weight of conventional solid beams. While their solid
top and bottom provide great strength,
the center is cut out at intervals to lighten
the beam and to form tie-offs or hand-holds. When planning to build such a
beam, consider the potential uses and
make the cutouts large enough to accommodate a gloved hand, four Fingers of
which should slip easily through the
holes.
There are two different methods for
building exterior beams, both of which
have worked well for us — lamination,
which involves epoxy gluing thin strips to
build up the beam to required size, and
sawn beams.
Laminated & Sawn
Decks and sweeping complex shapes
make good use of laminated beams,
which can be built from smaller strips and
pieces to save money and can be made to
conform to just about any shape (Fig. 2).
If you plan to build only one or two
beams, it will probably be easier to glue
them right in place on the boat than to
build a laminating form or strongback.
Figure 2
If a number of beams are needed and
the deck or cabintop maintains the same
curvature, then it may be worthwhile to
build all the beams on a laminating form.
One like the bracket form shown can be
easily changed for various shapes and can
also be used to build beams right from
the lofted lines of the boat (Fig. 3). This
ensures accuracy and allows the beams to
be built before the boat is completed and
put in place later.
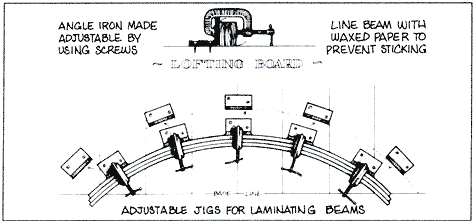
Figure 3
We lay a sheet of plastic over the boat or
form to prevent the beams from sticking,
then remove the beam for finishing when
the epoxy has cured. PreFinishing "on the
bench" is always faster and produces
superior work. After all possible finishing
is completed, we glue the beam in its
proper location.
When laminating beams, make the
laminations thin enough so that you don't
need excessive force to hold them in
place, but don't make them so thin and
flimsy that too many glue lines are
required. Most deck cambers will take
1/2-inch or 3/8-inch laminations, but radical
shapes may require using laminations as
small as 1/8-inch veneer, which will conform to a very tight radius.
After laminating the entire beam, remove it from the cabintop, deck, or laminating form and clean off the sides by
planing and sanding. Laminating with
strips slightly wider than needed in the
finished beam allows us to clean off the
glue drips and still end up with the proper
width. The top edges should be rounded
with a 1/2-inch or larger radius to make them safer on deck should you fall on
them. Also, make any cutouts at this time
using a sharp blade in a jig saw, and round
the edges of the holes using a router bit or
wood rasp.
Beams may also be tapered from top to
bottom lo save weight and achieve a less
bulky look. Tapered beams can look very
clean and finished where parallel sided
beams often look bulky and clumsy.
Plywood makes the best sawn beams,
especially if there is an extreme or unusual shape to which the beam must conform, since optimum strength is provided
by the multiple opposing laminations of
veneer in the plywood, lf there is minimal
shape in the beam, wide lumber will also
work well, but plywood is preferable for
maximum strength to weight. We build
plywood beams by cutting a pattern to
shape, scribing it right to the deck or
cabintop location. Then we cut out and
glue together as many thicknesses as
necessary for width, finally finishing it,
and attaching it to the deck.
Permanent & Removable
If you plan to attach the beams to the
boat using bolts through the deck or cabintop, you can use those same bolts for clamping pressure while laminating and
then for permanently attaching the beam
in place. A fastening alternative for
smaller beams is to simply epoxy glue
them in place, after which all fastenings
can be removed.We routinely glue wood
to gelcoat and fiberglass laminate using
WEST system brand epoxy. Both sanded
and cleaned surfaces are wet out with
catalyzed resin, then a thickened mixture
of epoxy is applied to one of the mating
surfaces. This provides a bond so strong
that we routinely remove all fastenings.
If you want the beams to be removable,
they can be bedded and bolted in place.
Carriage bolts work well. Countersink the
heads and seal the holes with wood plugs
bedded in silicone. Removing the plugs
for access to the bolt head or nut will
probably destroy the wood plug, but they
should be renewed each time anyway. To
easily remove such a plug, drill a small
pilot hole through its center, then insert a
wood screw into the hole and tighten.
The screwwill enter the plug and bottom
out on the head of the bolt. As you continue to tighten it, it will lift the plug right
out of the hole.
For permanently attached beams, we
also use epoxy fillets on the edges (Fig.4). This seals the edges of the beams from
moisture, looks good, creates a stronger
bond between the deck or cabintop, and
increases the bearing area of the beam.
These fillets look very good after they are
painted, and the beams seem to grow
right out of the boat.
Figure 4
PAUL and MARYA BUTLER are the authors of
"Fine Yacht Finishes for Wood and
Fiberglass Boats" and
"Upgrading Your
Small Sailboat for Cruising",
published by International Marine.
|