Shortly after submitting the article “American Ingenuity” to Duckworks Magazine, an item appeared on the local news that Albuquerque’s “Great Race down the Rio Grande” would finally be run in 2008, after a 13 year hiatus that had been caused by low water in the Rio Grande. Dad and I looked at each other across the room and both said “let’s do it”. This sparked the concept for the next PVC and duct tape boat (PVC version 4).
A limited time frame, 19 days, and a desire to keep costs low presented challenges to be overcome. The boat would have to seat two and have a skin more durable than the 4 mil plastic used to test the single seat boat design. We worked out the basic design and began construction over Memorial Day weekend.
The final frame was 16-1/2 feet long and 3 feet wide but used the same construction ideas as the single seat boat. The additional features were the cockpit frame and decking. The cockpit used a new type of attachment bracket shown below.
The final frame
click images to enlarge |
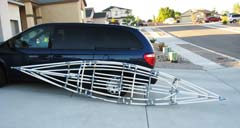
|
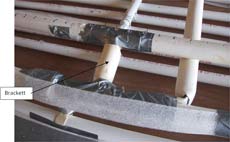
|
New Bracket for cockpit frame |
The photo also shows the holes drilled in the cockpit frame for sewing the skin to the frame and plastic foam used to pad the contact between the skin and frame. I had read that this would reduce damage to the skin by reducing friction between the frame and the pipe, and it served its purpose well.
On May 24th we took the frame down to the Rio Grande, skinned it with 4 mil plastic, and put it in the water to test the basic design. It floated reasonably well, but we did notice two things that needed improvement. The forward seat needed a backrest and the bottom stringers needed a different method of attachment, especially in the areas where we would be stepping. The duct tape-bracket combination did not perform well under tension.
To solve these, we made a seat back from a frame recycled from PVC version 2 and support of PVC pipe held in place with scrap double-sided Velcro. The floor stringer issue was solved by lashing the stringers to the frame with nylon mason twine. Holes were drilled into the PVC pipe for the lashings to prevent the lashings and pipe from slipping as the construction of PVC version 1 had shown us that this was crucial.
The lashings on the frame that connected the stringers |
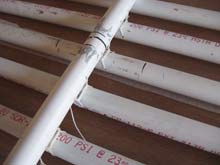
|
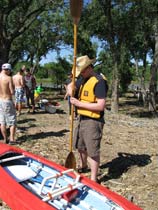
|
Me assembling my double paddle |
We were left with 6 days to skin the frame. Old bed sheets were sewn to the frame with nylon kite string and coated with old latex house paint. A second skin was sewn over the first for durability. We were not sure this was necessary, but figured it would not hurt. The idea was that the inner skin layer would still be water tight if the outer skin punctured. This was a much more permanent skin than we had intended for a duct tape boat, but it proved to be extremely durable and is still in full operation.
We had previously run a few tests with different fabrics and paint and had determined that gloss exterior house paint was the most flexible. The basic strength of the skin is a function of the base fabric. This meant that bed sheets would not be ideal for a durable skin but should serve for the race.
We had originally planned to place a layer of window screen between the layers of bed sheet to help prevent tears to the inner skin, but realized this would weaken the thin sheets. Eventually, we put a few pieces of old upholstery vinyl between the sheets in the bottom “rub areas” only to prevent severe puncturing of the inner skin. The painting of the skin was completed by Thursday night.
Saturday we got to the launch area at the river with our boat registered as a homemade craft. We figured that this would be a good time to test our basic boating capabilities since there were plenty of rescue personnel around. We also decided that if we only got 100 yards and sank, we would have at least tried and would have learned something, no matter what the outcome.
Approaching the finish line |
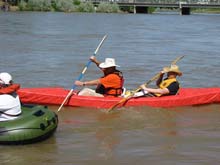
|
I’m not sure how many home made craft launched before we did, but we just wandered down the river, admiring the scenery and unwieldy other water craft, and generally having fun. Seven miles later, at the exit point, we discovered that we had taken first place in the homemade craft group.
Later we discovered that two small areas of the skin had the paint rubbed away on some sandbars, but no tears were evident. We do not plan any more boat building this summer, but we have put the boats to good use for fishing. After all, that was the original purpose for our boats.
At the inspection/judging area for homemade craft, while we were waiting to launch, my mom said she heard many comments, such as “PVC pipe and duct tape? No.” “Yeah, go check it out.” The comments continued after the race.
Dad had previously developed a skin hole patching technique using paint and fabric. We apply a bit of paint around the hole, place a piece of fabric over the hole and then paint the patch. This has patched both the PVC and bed sheet boat and the skin on our 40-plus year old Folbot with its original skin.
*****
|