Making Tapered and Beveled
Stems for the Seaclipper 20
To date, all my boat projects have been monohulls. But, I’ve
dreamed of building a trimaran for a long time. In the spring
of 2010, Jim Brown and John Marples introduced their plans for
the new trimaran design called the Seaclipper 20. As soon as I
read about the boat and reviewed the study plans, my eyes lit
up. Finally, here was a trimaran project that matched my skill
set, could be built within a reasonable time budget, and matched
the kind of day sailing I wanted to do. I ordered the plans and
started to build in June.
The amas and main hull of the Seaclipper 20 use stems that are
tapered and beveled. Many other boat designs also use tapered
and beveled stems. So, even if you are not building a Seaclipper
20, this article still may be of interest to you.
Making parts that are only beveled or only tapered is relatively
easy. But, I found that making stems that are both tapered and
beveled was nontrivial for me given the tools I have in my shop.
I tried four approaches. The first two didn’t work. The
third worked, but was complicated and time consuming using mirror
image patterns on a taper jig for the table saw. The parts that
emerged from the third effort were fine, but unfortunately made
from red oak. John Marples advised that red oak moves and is often
not a good friend of epoxy. So, I used a fourth method, described
here, to make stems from more suitable wood. The method is easy
and fast, even for me. More importantly, I felt comfortable with
the method and did not ever feel that I was testing the envelope
of reasonable safety.
 |
Fig. 1. It's still early in the building process,
but already the parts are piling up. These are the bulkheads,
transoms, stems, and butt blocks, for all three hulls. The
big main hull bulkheads and transom are buried at the bottom
of the pile. Also shown are the daggerboard blank, and rudder
blank. Not shown are the stringers, ribs, and daggerboard
box. |
 |
Fig. 2. The steps in this article show how to
make tapered stems like this set of two ama stems and the
main hull stems. |
I used a Festool saw and guide to make the stems. The Festool
guide and similar saw guides positively restrict the saw to move
along a linear path only. These guides do not allow the saw to
drift from the intended line unless something really awry happens.
Before you lose interest on grounds that you don't have a Festool
saw, the method described here will work for any circular saw
guided by a straight edge that positively holds the saw to a straight
line. I don't think that I would recommend this method with a
mere straight edge that allows the saw to drift without positive
control. The drift doesn't affect the workpiece since the drift
away from the guide is into waste. However, saw drift while ripping
or even crosscutting is not safe, particularly with thick wood
blanks used to make stems.
Here is the method step by step.
Step 1: Make your blank(s) from suitable stock and layout your
stem pattern(s) full size on the blanks.
Step 2. Drill two counterbores in the stem for mounting screws.
See Fig. 4. I drilled counterbores that were 3/4 inch in diameter
to fit the self-tapping Kreg screws I used for mounting the stem
blank to the work table. Later these bores and the screw holes
will be filled with epoxy.
Step 3. Grab some scraps and make the work table shown in Fig.
3. If you screw your head blocks to the table, position the screws
well to the outside and make sure that your saw path will never
hit them. In Fig. 3, my head block at the top of the table is
way too short. I had to use a supplemental block to help support
and clamp my saw guide to the table.
Step 4: Mount the blank to the table using self-tapping screws.
I like Kreg screws for this. Position the blank so the cutting
path runs up the table center and not through any screws on the
outboard ends of the support blocks. The wide face of the stem
faces up. You can position the stem blank anywhere you want so
long as the saw blade path misses the screws. The main stem is
36 inches long, so this table is long to accommodate that stem
as well as the shorter ama stem shown in the Figures.
 |
Fig. 3. The simple work table takes only a few
minutes to build. Blocks of wood are screwed to a ¾
inch scrap 2' x 4' MDF sheet or other board. The screws are
well to the ends of the blocks so that the saw path never
goes near them. The blocks support the saw guide and are the
same thickness as the stem blank. The stem blank also is screwed
to the table. |
 |
Fig. 4. The stem blank for an ama is screwed
to the table. Precision is not needed for this at all, because
the saw guide will be aligned to the cut line and not vice
versa. The stem pattern is laid out full size on the blank.
Two screws do the job of holding the blank to the table. The
screws are recessed in counterbores so they don't interfere
with the saw guide. |
Step 5: Clamp the saw guide to the table, aligned with the desired
cut line. Both ends should be secured as we will need to make
multiple passes. This Festool saw has a lot of power and can crosscut
a 2 x 4 easily, but the saw has to work way too hard to rip this
tapered bevel in one pass. So, I used four passes, cutting deeper
by about 12 mm (about ½ inch) with each pass. Because the
saw guide keeps the saw on line, each pass goes successively deeper
on the same cut line as long as the saw guide is not moved between
passes.
Step 6: Set the saw depth for the first pass, about 12 mm. Place
the saw onto the guide in position and make the first pass. Then
increase the depth of cut about 10 mm to 12 mm with each successive
pass until the cut is complete.
 |
Fig. 5. Secure the saw guide in position to
make the bevel cut. The guide is clamped at both ends to avoid
movement of the guide during the cut. Note how the guide is
aimed down the workpiece to cut the taper down the workpiece
length. |
 |
Fig. 6 . The saw is placed into position on
the guide. The saw is set to the bevel as specified in the
plans. |
 |
Fig. 7. The first pass is complete. The saw’s
cutting depth is successively increased adjusted to make 2d,
3d, and 4thpasses. |
 |
Fig. 8. After the 4thpass, the first beveled
taper is complete. |
Step 7: We want to make a stem with a cross section that is a
trapezoid, not a parallelogram (I almost made some parallelograms).
So, we need to remove the stem blank and remount it to make the
proper cut. Remove the screws to free the blank. Turn the blank
around so that the end that was at the head of the table is now
at the bottom. The wide face of the stem is still facing up. If
you do this right, the first bevel is now on the left and new
bevel to be made is on the right.
Step 8: Secure the saw guide in position. Remember to clamp the
guide at both ends so there is no movement of the guide during
the multiple passes used to make the cut. Make sure you are cutting
on the desired line and not the center line (I almost did this,
too, on one stem). Double check to make sure the saw will not
hit any screws at the foot or head of the table. If there is a
screw in the way, you will need to move and remount the stem blank
to avoid this.
Step 9: Again using four passes, cut the second beveled taper.
Your stem is now done and can be removed from the table. The holes
made in the stem for the counterbore and screws can be filled
with epoxy to protect the stem from rot.
 |
Fig. 9. To make the other beveled taper, the
workpiece is removed from the table, flipped around, and remounted
so the first beveled taper we made is on the left and the
new beveled taper to be made is on the right. |
 |
Fig. 10. Here’s a close up view showing
the stem blank remounted correctly. Note the wide face of
the stem is still facing up. We flipped the stem around. We
did not flip it over. |
 |
Fig. 11. The stem is now complete and can be
removed from the table. |
 |
Fig. 12. The quality of the beveled tapers is
very good, as can be seen in this end view. |
*****
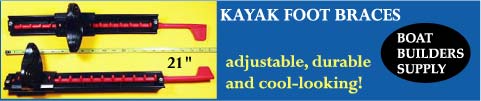
|