To
Part One
To Part Three
Well things have moved along at a frightening rate, at least
for Mark Bowdidge, (Bowdidge
Marine Designs), the boat has progressed very quickly.
After the first month, the hull has been glued, turned over,
and the internal joins glued and filleted, the seat boxes have
been fabricated and floors cut and all panels pre-cut.
Precutting the panels speeds the building process, as you have
everything on hand ready to use, with out stopping to cut the
next panel.
The seat boxes are now fitted and coved in, and glassed, as well
as the foredeck and front bulkhead, all the hatch openings were
pre-cut and ring frames glued in before fitting.
The inside of the hull was given a saturation coat of epoxy (BoteCote),
and I then started, with the fitting of the floors and quarter
knees and transom support. The floors are supported by 18mm x
11mm stringers at 150mm centres, and are solid as a rock. The
side pockets were fitted at this point extremely handy to hold,
knives, measuring sticks and misc bits and pieces.
After getting the interior fitted and glassed, it was time to
turn the hull back over, and start on the outside, the zippy ties
were cut off and the hull sanded, glued and coved, this hull is
a little more involved, with extra panels, in the reverse chines.
It makes for an interesting hull shape, with very good underwater
lines.
The hull has now been filled sanded and filled again and sanded,
then glassed with 200grm glass and BoteCote epoxy, I found that
if the first coat of resin was broken down with TPRD at the recommended
rate, the glass wets out very quickly, with minimum of air bubbles.
Gunwales are now fitted, this proved to be interesting as they
are 31 x 11mm hoop pine I found that it was necessary to laminate
the bow sections, both inner and outer, due to the curve and angle
of the panels.
A word of warning about resin and glue, it pays not to mix too
much at a time (EXOTHERMIC REACTION), the resin is better off
in a shallow tray than a deep container. The same applies with
glue and filler.
To cut a long story short, the hull has now been glassed and
faired, with two coats of undercoat applied, here I have used
Norglass and will be using their marine enamel for the final finish.
My wife is happy with the result to date, which is a very necessary
thing if the minister for finance is not happy, watch out as the
purse strings suddenly become very tight.
Also this is an important point for this design, I can lift the
bow or stern above my head, the design weight is 60kg, and I think
that I am within cooee of this, (good design work Mark) with only
some deck hardware to fit and the final painting to be done.
Builders plate has been acquired and engraved, rego papers filled
out, we are go for launch on schedule, MR MURPHY KEEP AWAY, or
I curse you with a BANSHEE.
Mangrove
Jack design by Mark Bowdidge is available at Duckworks.
*****
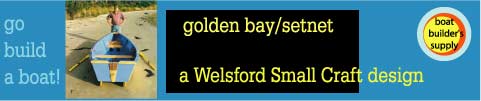
|