Last part of this article I told you all of my fine theories. Well, let’s see how these ideas shaped up in practice. The first job was to raise the ‘boatshed’ roof 2’ to accommodate the extra height in the fore part of the boat. For the wheelhouse a further lift of about 5’ will be needed.
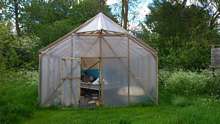 |
We go from this cosy snug little shed … |
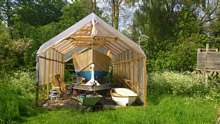 |
… to this extended structure, fortunately it is summer so the extra ventilation is welcome. I hope by winter to have the boat watertight and the shed finally removed. |
As always you need a place to start, and this was my starting point…
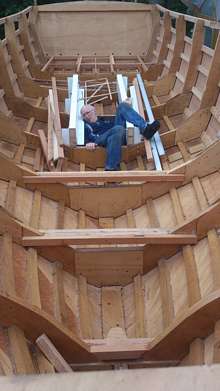 |
No - not drunk in the bilges again, just trying to get a line of sight on the three cabin floor supports before I finally glue them in place. |
Having got the fore cabin floor joists sorted I then turned to the roof line. It was still a bit too high, so I tried to jiggle it into place, taking an inch off here and there and adjusting the angles until I was happy with the size. As standing room was not required at the front I sloped it forwards slightly. When finished the boat will definitely look more Landrover than Lamborghini due to the high fore-cabin, but I do want sufficient headroom and floor space so something has to give. This can always be moderated and disguised, to some extent, with colour and window placement.
I usually create my own solutions and then consult the experts, sometimes we agree, sometimes not! In this case I bolted the 2” x 1.5” frame extensions using stainless steel bolts. As white oak can be quite aggressive with ferrous metals I decided to drill at 12mm to take the nylon shoulder washers used on the trailer and also wrapped the shaft of the bolt with a spiral of sticky tape, a Nyloc nut and two stainless steel penny washers complete each fastening, two bolts per piece of wood. It took a bit of adjusting before finally gluing it all together with some small scrap pieces of fibre glass as spacers to hold the glue, and to tie the joint.
The laminated roof beams I made in a previous article were glued in place with cheeks either side to strengthen and hold the joint while it dried. The next part was to cut the outer edge of the joints, where the roof and sides meet to take a small fillet of wood, to provide a wider gluing surface, neater finish and hold the edges of the plywood together with a few screws. This job required three pairs of hands, but as only one was available a knee, an elbow some cramps a couple of Spanish Windlasses and a lot of cussing were also employed to hold the wood in place. As I want a strong roof for several people to stand on, extra roof beams are deployed midway between the frames - except for one spacing, which is 2” less to accommodate the plywood roof join at 4’.
When joining wood together in this way, the initial structure can seem quite flimsy, though not so much in this case, but it soon stiffens up when other pieces are added at right angles and a surface of plywood is added.
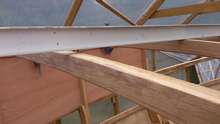 |
Now how the **** did that gap happen. |
As always the theory trips off the tongue fully formed with neither a crease nor a wrinkle. The practice on the other hand always comes with warts, carbuncles and many other imperfections. This structure was built in stages, so even though the framework was exact as soon as I applied the side cheeks it was under tension due to the plywood trying to straighten, causing the end beams to be stretched and the centre beam to be compressed. Never mind I can plane some off the ones standing proud and pack this one a bit. It doesn’t help having the cabin deck sloping forwards as there is also a small triangular gap at the rear edge of each beam which will need to be planed out and maybe some filler applied.
Due to a slight lack of accuracy, on my part, in laying up the hull, the fore cabin came with a slight warp. A further over-zealous twist of a Spanish windlass also gave the structure a slight kink at the rear. Fortunately these defects are not noticed by the casual observer, I could rectify them but am quite happy to overlook them. Apart from these minor blemishes the whole structure is very satisfactory and pleasing to the eye at this point. My only concern is that it is starting to look rather tall – think low bridges and windage.
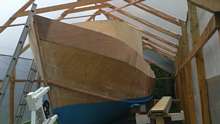 |
The result so far. Just needs the edges rounding over and screw heads filling to be ready for fibreglass. Looks like I will have the boat watertight for winter. Doors, hatches and portholes will be made next year. |
Having got this far I turned my attention to the next job, only there seemed to be several of them vying for attention:
- Upper strakes, full length of the boat.
- Side decks at the front (though hardly a deck at 3” wide)
- Fore deck and Samson post.
Number 1 was out as it was convenient to use the lower side rail as a step for the moment, when climbing into the boat, also I need to seal the backs of the frames with epoxy while there is still easy access. Number 2 was out as I would prefer to overlap them on number 1 and was planning to use the offcuts from this job. This left number 3.
Although I haven’t fully designed the fore deck yet it will need a Samson post. Having a Samson post on the fore deck will give the boat that tough and jaunty air that says ‘don’t mess with me, utility comes first here!’ Apart from looking good it is an extremely useful item to have on a boat. I didn’t have one on my catamaran, and was constantly anxious about the strength of the deck cleats and the stress I was putting on them. The first job was to do some research and find this excellent article our very own Duckworks website. It all sounds a good idea, particularly the chain snubber. But how do I fit it to my boat? It has to go pretty far forwards to prevent the length being too long and it interfering with foot room for the bunks. It would be good to make it with oak, but I don’t want to spend a lot of money on the metal fittings which would preferably be bronze, so it will be made from kerouing (apitong) which compares with teak for strength but stiffer and more resistant to shock loads (ideal for a Samson post) it is also resistant to crushing loads and won’t rot stainless steel fittings and screws. If my winch post is anything to go by it will also weigh quite a bit. I recon 3½“ square should be about the right size.
Now how about some design of the fore deck:
- It will need two oak beams, one either side of the Samson post to hold and brace it.
- I will have to decide where the fairleads will go and how many, to build in extra blocks under the deck.
- The Samson post must be removable for repair and replacement and will need to integrate with the anchor board. Sealing it in place with epoxy will not work due to the movement, so a final seam of mastic must be used on top of the epoxy to make it watertight.
- I will be putting a pulpit rail at the front eventually so some account must be taken of the location and deck strengthening.
- Should I use an anchor rode or all chain (bearing in mind the final weight all up must under 3.5 tons for legal towing).
- Do I want an anchor locker built into the deck, a chain tube into the bilges (could be messy and difficult to clean, not to mention the smell) or a locker on top to act as a seat in front of the fore cabin? The anchor itself will sit on the anchor board.
Not easy! My approach was to sit on the newly made cabin roof and ponder for an hour. Eventually some vague notions began to take form and I envisioned sitting here relaxing with a glass of wine as the boat slowly motored in crystal clear waters on a warm balmy evening (totally ridiculous, of course, as we don’t get days like that in Britain, or water), so I would need a seat and that can be used to house chain, rode, scrubbing brush, bucket – all the essential anchoring components. The seat would not be full width to allow for stowage of fenders either side on the pulpit side rails. Leading mooring warps forwards would pose no problem, but leading them aft would require a fairlead each side by the cabin corners, so that is where extra deck plates would be needed. I definitely don’t want smelly chain in my nice clean bilges and can’t afford the extra weight of all chain, so 30’ of chain and the rest rode. Its amazing how one decision leads to the next and pretty soon the whole thing is designed. If only putting it into practice was that easy!
The fore deck worked out well and integrated nicely with the cabin front. First step was to laminate the Samson post, I decided to go with the kerouing for a number of reasons, one being that it is not so brittle as oak and copes well with shock loads, though at 3½” square, you should be able to hang the boat on it whatever wood you choose - provided the foredeck will take the strain. As it is removable it can always be replaced when the time comes.
My first thought was to attach it to the stem at about 4’ length, on reflection however it turned out better to brace the post on the upper breasthook and seat it on the lower one, giving a length of 2’ and hence an extra 4” foot room for the bunk. It is so important when you are the designer, to ponder all the options and plan ahead so the result fits together well and works elegantly. Speaking of elegant, the post supporting structure was not one of my finest creations. In fact it was all held together with glue and stainless steel bolts and packed with offcuts. I think it will be strong enough under all loads, but it just looks clumsy.
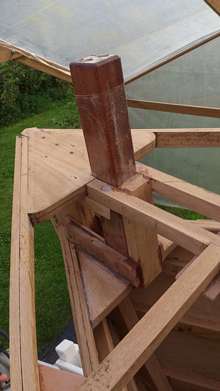 |
Structure of the fore deck showing how the Samson post is braced. The best decision I made was to leave the upper strake off for the moment for easy access. |
The next part of the design was the wheel house, given that I had already completed the fore cabin, this structure is just the same but higher and with a wider side deck on the starboard side. Of course I will need to take into account the forward raked windows, doors and visor.
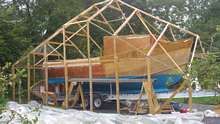 |
Boat shed remodelled yet again to accommodate the new bridge plus working space above. The biggest difficulty I have is not being able to see a long view of the boat like this when the cover is on. |
Having left a gap here in writing this article for 6 weeks I am now writing in retrospect and can say that this part didn’t turn out how I planned. The intention was to have a single enclosed space with a wide side deck on the starboard side, but the height of the fore cabin necessitated a raised bridge, leaving very little for the aft seating area by the time the 15” side deck was taken out. Having a trawl round the internet I spotted a Legacy 32 for sale and the pictures showed just what I could do with the bridge, which let’s face it, will be a much used space. As I have a side door on the starboard side the extra wide deck was no longer needed aft of this point, so out came the jig saw and off went the side deck – it’s never too late for a change of mind when only a couple of pieces of wood have been glued.
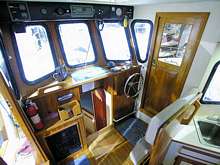 |
Bridge of Legacy 32, what I hope it will look like when finished. It’s always a good idea to look for pictures on the internet before starting to design. |
Now what about trying to moor on the port side single handed in a current - say on a river. Not so easy with only one side door on the other side. Also the boat would look better from the port side if it had a door to define the bridge. I decided that the space was more valuable inside and so only allowed enough width to place a bollard and sliding door.
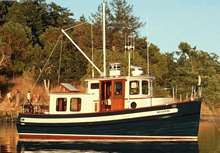 |
Another picture I love of an older Nordic tug 26, Sod the cost and work of varnishing I WANT doors like this. |
Now the boat is starting to look more like the Southwest Retro Marine Trawler 25 – I may or may not put in a dummy funnel to gain headroom when stepping down from the bridge.
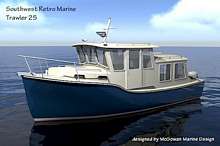 |
Not a bad look, you can’t have everything in a 25’ boat, or if you do some bits are going to be rather small. |
What I ended up with so far! Sorry about the picture, it’s difficult to get a long shot with this poly tunnel over the boat. Not quite what I had planned when setting out, as the design has evolved since then, partly due to inspiration and partly due to necessity.
Overall I am very happy with it. It just needs a coat of fibreglass to make it watertight for the winter. As the covering has been taken off the boatshed so many times for upgrades I have some snags which leak and as the shed is now so tall and the polythene getting old a big storm may damage it so a watertight boat would be desirable. Also it may be a good idea to keep the shed over winter for extra protection and so that I can paint the exterior undercover next year.
So if you have read this far I recon you are probably looking for information/inspiration, so let’s see what advice I can give for those of you in similar circumstances:
- Don’t be afraid to give it a go yourself, if you get stuck you can always ask for advice or pay for professional help.
- Do as much research as you can beforehand. I find Google images provide a lot of inspiration and ideas.
- Do base your boat on a sound pedigree, companies like Glen-L, Bateau and Duckworks have many designs, several of which may give you 85% or 90% of what you want.
- If you are designing yourself, you should be prepared to redo bits that don’t work out or if you think of a better way to do things.
- Don’t even think of something like this unless you have the patience of a saint and the tenacity of a limpet, these are qualities you will need, as well as a deep wallet. But you can build a lot smaller and get just as much fun.
- Above all try to enjoy the process as much as possible while you can, after all YOU made the decision to build it.
*****
Click HERE for a list of articles by Mike Machnicki
|