Part 1 - 10 pound 14 Footer
Overview
I wanted to build the lightest possible kayak so I could do some lake portage trips and carry the kayak comfortably under my arm over the portages. It also had to be packable, so it had to be a folder. Weight was a greater consideration that durability. I thought 10 pounds would be about right, and the final weight ended up just about exactly that.
Design
Coming across Tom Yost's Sonnet 14 design for an inflatable kayak, I realized it was a great starting point and that I could reduce the weight by substituting lighter materials and simplifying the design a bit. I made the stems straight and vertical and eliminated the hull side taper. The result is a rounded box shape in cross section.
Tom's design consists of the skin, a keel tube and a separate side frame that keeps the sides of the boat apart. The sponsons fit into sleeves built in to the inside of the skin on each side. The main alteration I made to this arrangement was to sew the pairs of sponsons together along the weld seam. This eliminated the need for the sponson sleeves, as the side frame would now push against the seam between the sponsons. The sponsons position themselves naturally with this arrangement.
Materials and Construction
For the skin I wanted the lightest material I could find that would stand up reasonably well under careful use. I chose material made by Cubic Tech Corp, often referred to as "Cuben Fiber". Specifically the 3 oz/sq yd CT5K.18/wov.32c, which has an opaque polyester covering on one side. This material is very strong and completely waterproof. Its Achilles heel is abrasion resistance. So I added Aquaseal along the keel and at the stems for reinforcement.
To save as much weight as possible, I used carbon fiber for the keel tube, which needs to resist a lot of bending, and large tent pole tubes for the side frame.
I used 13'-5" Folbot sponsons, just as in Tom Sonnet 14 design.
One critical factor for me was I had to be able to build the kayak in my bedroom, specifically at the foot of my bed. It was the only free space available. I was lucky that it's a large room and the free area was about 6 feet x 17 feet. It was also important that the boat could be built with only a few simple hand tools and no messy or smelly adhesives, as I had to sleep in the room every night. It turned out all I needed to build the boat was a hacksaw, hammer, power drill and a pair of scissors. Oh, and a few rolls of tape. The beauty of Cuben Fiber is that strong watertight seams can be made with double-sided tape. The tape I used was 1" wide 3M 9472 LE.
With the exception of four small metal snap buttons, the boat has no mechanical fittings of any kind (like bolts or screws).
Patterns
Rather than building a strongback frame and laying the material over it for cutting, my boat skin was made like a pair of jeans, by making a pattern and tracing it over the material. This may not save work, but it substitutes up front figuring-out for building-stuff-later. As a engineer/computer type, this suits me fine. After a little simple math and use of the free 3D modeling software Blender, I had offsets for the patterns. I laid them out on Tyvek construction paper. Since there was no slope to the sides or stems, the top and bottom panels of the skin were identical. So I just needed two patterns, one for the top/bottom and one for the sides. And since the design was symmetrical front to back, I only needed to make patterns for one half the length of the boat. I added a one inch seam allowance to the top/bottom pattern and traced the patterns on the material.
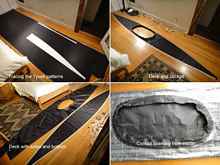 |
The Skin
After tracing and cutting out the four skin panels I was ready for one of the only two tricky parts of the construction. First was the cockpit coaming. This was difficult because it involved attaching an oval cylindrical shape (the coaming) to a flat sheet (the deck). I ended up creating a flange-like seam that was cut about every inch or so all around the coaming and taped to the underside of the deck. After the coaming, seaming the rest of the skin was very straightforward. The result after finishing the four skin seams was a long tapered tube with open ends. The next step was the second tricky bit: closing the stems.
I built a wood form that I could stuff into each end of the skin to provide a solid surface to work against while folding and seaming the skin to close up the ends of the boat. I folded the ends of one side panel around the stem so that it overlapped with the other side by two inches. This was seamed with the double side tape. Eventually I would cover the stem area with Aquaseal to fully seal it and add some reinforcing.
The Keel
The keel is 1 1/8 inch carbon fiber tubing purchased from The Carbon Tube Shop online. This is very expensive material. Did I mention that cost was not an object for this project? I ordered it cut into four 26" and two 29" pieces. I also ordered 6" ferrules to join the sections together. The keel halves would be joined in the center with a long aluminum sleeve.
I used short pieces of aluminum tube for the stems and joined them to the keel with nylon elbows. Everything is so much easier with ninety degree angles!
The Side Frame
The side frame is made with Easton tent pole tubing, purchased in 26" lengths. I discovered I could join the 0.49" tent poles with 5/8" nylon barbed hose tees, which are plumbing fittings available in marine supply stores. They were almost a perfect fit. I had to ream them out slightly with a 31/64" drill bit. Then I found if I immersed them in boiling water, they softened and could then be tapped over the tubes with a hammer. When cooled, the fittings make a very tight fit.
The Sponsons
I used four 13'-5" Folbot sponsons, sewed together in pairs along the weld seams. When the boat is assembled, the side frame is positioned along the seams. The crossbars hold the side frame out against the sponsons and the skin tensions when the sponsons are inflated.
The Cockpit
To make the seat as light as possible I use two Neoair inflatable camping seats, one for the seat and one for a backrest. They weigh about 73 grams each. Two pieces of 1" foam on each side of the keel tube creates a flat base for the inflatable seat. To support the seat back, I added two extra cross tubes to the side frame at the rear end of the cockpit. The bottom one comes apart so I can more easily stow gear behind the cockpit.
As a proud owner of an Alpacka Yukon Yak packraft, I knew that Alpacka sold sprayskirts for their boats. So I bought one of these, along with their super light coaming ring. After trimming a few inches off the ring, it fit my 34" x 18" cockpit opening perfectly.
Assembly and Packing
The boat goes together in 15 or 20 minutes. It packs up in about 25 liters of space.
In Use
I used the boat for a 54 km lake paddle with 8 km of portages the summer of 2014. It worked very well and was very easy to carry as expected. I use the keel tube as a handle. It even performed well with some chop and headwinds. At the end I did have a few very small leaks under the stem knuckles. This was probably due to leaving the boat in shallow water to rub back and forth over rocks and sand while I scoped out a camp sight. Bad idea. However, the leaks were easily fixed by reinforcing the area with extra Aquaseal when I got back home.
Contact: tim_evans@shaw.ca
www.cubenmaker.com
|