We are making very good progress on the two
12-foot Grandy skiffs we are building in the Traditional
Small boat class at the North West School of Wooden
Boat Building in Port Hadlock WA.
We have fourteen people in this class. There are four
who are in their fifties (several of whom are retired),
three in their thirties and forties and seven who
are in their twenties (college grads, veterans, and
high school graduates). It is a congenial group, and
one that enjoys (or can tolerate, anyway) a wide range
of eclectic music in the shop!
Since my last note in mid-January, we've finished
and leathered the oars, completed the lofting, constructed
the molds, stem, transom and keel, and are ready to
begin planking the boats.
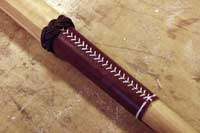 |
Leathered oars |
The lofting was completed on two sheets of 4x8 plywood
doorskin (very thin plywood), painted white. From
start to finish, it took the student lofting team
just under two weeks to loft the boat, working 5 hours
a day, more or less. (We spend two hours a day in
classroom sessions, and about an hour a day in shop
instruction). The lofting team is certain they could
halve that time on the next boat of similar complexity.
The student lofting
team |
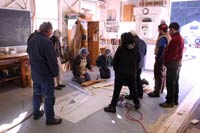
|
The lofting provides the builder the information
needed to construct most of the essential parts of
the boat. From it, we built the backbone (stem, keel
and transom) assembly and the molds.
The patterns for each piece of the backbone and the
molds were carefully traced on mylar from the lofting.
Then, the mylar was secured to the stock and the pattern
pricked through with an awl, then drawn directly on
to the stock. Here, a student works punching the pattern
through the mylar onto the mahogany stock for the
transom.
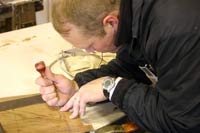 |
Carter punches
the lofted pattern through the mylar onto the
stock. |
The piece was cut out and compared to the lofting
again. Minor corrections were made, and the pieces
nailed, glued and screwed together right on the loft
floor to ensure each mold is as perfectly matched
to the lofting as possible. Here, a mold is constructed
on the loft floor. It is fussy work.
Jeff and Alicia
building molds on loft floor |
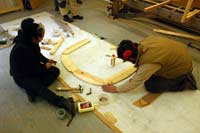
|
While the molds were being constructed, the same
process was being followed to build the backbone.
Here, one of the students chops the rabbet into the
stem. The rabbet is the groove in the stem and keel
into which the planking will be fitted. The small
piece of wood in his left hand is a fid, which is
the same thickness as the planking. It is used to
ensure the rabbet is of the correct depth and angle.
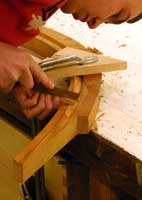 |
Matt cutting
stem rabbet |
We leveled the building frames with a water level
and erected the molds, which were carefully squared
to the centerline and braced.
Instructor Tim Lee
(left) and student Jeff setting up molds on the
building frame. |
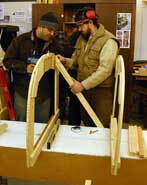
|
The backbone assembly was placed on the molds and
secured in place. You can see the transom is secured
via a temporary frame at this point to the building
frame. The transom's top rests on the temporary frame
to keep it at the correct height and angle.
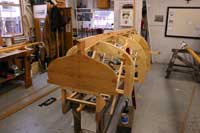 |
Keel, stem
and transom in place |
Slender cedar battens, the same thickness as the
lapstrake planks and the same width as the overlap
between the planks, were placed on the molds and tacked
into place. The battens represented the plank edges,
and were scrutinized to ensure the planking lines
were fair. The spring clips along the stem allowed
the battens to be easily adjusted. Elsewhere, the
battens were just finish-nailed in place, with each
nail driven only halfway home, again to facilitate
the inevitable adjustments needed to ensure fair planking
lines.
Instructor Tim Lee
explains how to line out planks. |
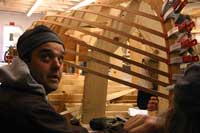
|
Then, vertical battens were placed both to lay out
the future location of the oak frames, and to ensure
that future fastenings will not conflict with each
other.
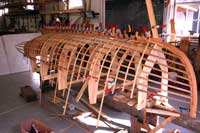 |
Lining out
planks and frames |
The boats are ready to be planked. We will plank
these boats during the week of 12-16 February 2007.
Sincerely,
Pete Leenhouts
Student, Traditional Small Boat Class
North West School of Wooden Boatbuilding
Port Hadlock WA
https://www.nwboatschool.org/
|